PROPER METHOD OF STORING
MATERIALS
Take care of your gear and supplies by securing or
storing them properly at the close of each business day.
his is especially important at sea since your ship could
encounter bad weather and rough seas at anytime. Keep
your supplies in good condition, out of the way, and
securely stored.
You will be responsible for a wide variety of
materials, including ecclesiastical supply items that
must be stored. Closed cabinets are preferable to open
shelves for storing supplies because they protect
materials from dust and damage. Store liquids or other
reproduction supplies so they will not stain other
materials if leakage or breakage should occur. Store
toxic fluids in a hazardous gear locker consisting of a
cool, well-ventilated place.
NOTE: In regard to toxic fluids, only a small
amount normally will be needed for each use.
Consequently, you should maintain only a limited
amount of these materials. There are regulations
prohibiting the storage of toxic materials in certain
locations on Navy ships. Check your commands
regulations and instructions concerning the storage of
these materials. Remember, being safety-conscious is
an attribute that every RP must possess.
In maintaining supplies, remember how important
cleanliness and order can be to safety as well as to
appearance. Accumulations of loose papers may pose
fire hazards. Plan cleaning periods and field days. Dust
desks and immediate areas frequently. This not only
makes for a more pleasant working environment but also
protects machinery and automatic data processing
(ADP) equipment from harm.
Label wrapped packages for easy identification.
Open only one package of each kind of materials at any
given time. his helps avoid waste and makes sure the
office of the chaplain does its part in using command
funds productively and responsibly.
USE AND MAINTENANCE OF OFFICE
EQUIPMENT
A basic responsibility of all RPs is using and
maintaining office equipment, whether it involves
calculators, typewriters, Mimeographs, spirit process
duplicators, dry electrical process machines, or
computers.
Your sophisticated office equipment probably will
require two levels of care. The first level is
manufacturer-suggested use and maintenance. The
second level can best be described as operator care and
troubleshooting.
Lets look at each of these levels,
starting with troubleshooting.
Troubleshooting
Manufacturers troubleshooting checklists can help
you resolve some of the problems you may encounter.
Manufacturers checklists include installation
checklists, feature checklists, and checklists that explain
normal daily operator maintenance. If, after following
the manufacturers checklist, you cannot solve the
problem, you may need to call a customer service
representative.
Servicing
Your operators manual will usually list the phone
numbers for customer service representatives. Before
calling your customer service representative, however,
you should gather certain information. If you have this
information readily available when you make the call,
the customer service operators will be able to help you
faster and more effectively. Specific information you
will need before calling includes the manufacturers
manual you are using, registration number of the
equipment, and any product information such as the
brand and type or model. If your equipment is a
computer, you may also need the name and type or
model of the interfacing equipment such as the monitor,
version of DOS, RAM memory information, printer, or
sheet feeder.
However well designed your equipment may be, it
will eventually need servicing. To do this there are five
generally recognized methods:
1.
2.
3.
4.
5.
A service contract with the manufacturer
A service contract with an individual service
person
Maintenance by Navy-trained service personnel
Use of the manufacturers service person on a
per call basis with no contract
Use of independent service personnel on a per
call basis with no contract
Machine servicing is clearly a matter of concern,
and the Navy usually chooses among these five methods
to keep its equipment serviced and in good working
condition. Without a service contract, however, the
tendency is to wait until something has gone wrong and
then the machine may be out of commission for days.
6-3
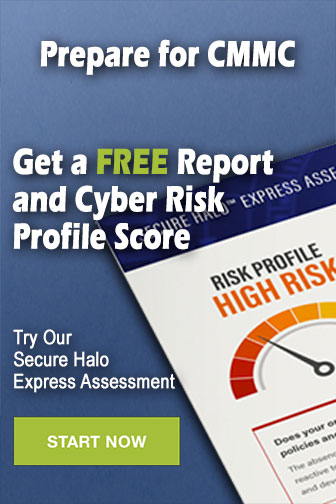